物理氣相沉積PVD Ti/TiN涂層提高冷沖模具壽命研究
發布時間:2020-05-26
1、前言
隨著汽車工業的迅速發展,汽車配套零件的需求量大幅度增加。其中,冷加工件的質量、產量和生產成本往往取決于冷作模具的工作條件及有效使用壽命。例如冷沖模具“控制臂翻邊凸模”(Cr12MoV),在大批量的生產過程中,大約經過2500次冷沖后就會導致冷沖件尺寸不合格造成報廢。經失效分析其主要原因是模具的摩擦學性能差,低的耐磨性和耐粘著性容易使模具的翻邊圓角和翻邊直壁磨損。為提高冷作模具使用壽命,在冷作模具上沉積TiN等硬質涂層是一有效途徑,采用離子氮化+物理氣相沉積硬質涂層則可進一步提高涂層與基體的結合強度及涂層的耐磨性,但由于模具工作條件的復雜性,所以在這方面的應用報道還比較少。
2、試驗方法和內容
2.1 試樣準備
以Cr12MoV為基體材料,加工成30*3*7mm3規格的試樣,經高淬高回熱處理(1100℃真空淬火和520℃×1.5h兩次回火),硬度為61HRC。再經砂紙研磨(從粗砂到03#),最后用W2.5金剛石研磨膏拋光。試樣在涂層前經嚴格的清洗、除銹和除油。
雙重處理涂層的制備工藝為:試樣先在LD-8100型離子氮化爐中進行離子氮化,氮化溫度500℃,氮化時間5h,真空度480~520Pa,工作電流30~40A。隨后沉積Ti/TiN涂層(工藝同單一處理)。
2.2 涂層表面性能測試
用HX-1000顯微硬度機,測定一系列載荷和(10g,25g,50g,100g,300g,500g,1000g)作用下的表面顯微硬度值。并且,在HITACHS-570電子掃描顯微鏡(SEM)和光學顯微鏡(OM)下觀察相應的顯微壓痕形貌,定性地分析涂層的表面承載能力及韌性。
用劃痕試驗評估涂層與基體結合狀況。本實驗采用半徑為200μm金剛石劃針(Stylus),以100N/min的加載速率連續加載,同時以10mm/min的速率劃過試樣表面,劃痕位移為5000um,在劃擦過程中,所加載荷由最初的10N增加到設定的60N。儀器同時記錄摩擦力-載荷等曲線。此外,使用OM和SEM觀察劃痕形貌,由此定性地得出表面與基體的結合強度大小。
2.3 磨損試驗
磨損試驗在MM-200型國產磨損試驗機上進行,以矩形涂層試樣(30*3*7mm3)為上試樣,表面等離子氮化的Cr12MoV鋼(1200Hv)滾輪(Φ40mm×10mm)為對磨試樣。磨損試驗條件為:沖擊式磨損(17次/min),轉速200r/min(線速度為0.42m/s),20#機油潤滑,載荷15kg,對磨0.5、1、3、6、9h,用磨損后的磨痕體積來衡量磨損量,計算公式為(1)式,同時利用OM和SEM觀測磨損試樣表面的磨痕形貌。

其中,V:磨痕體積,B:磨痕寬度,R:輪子半徑,L:磨痕長度。
2.4 應用試驗
3、結果和討論
3.1 顯微硬度試驗
圖1為表面硬度和載荷曲線,由圖可見,未表面處理(高淬高回)試樣的硬度值基本是不隨載荷的變化而變化,而單一處理和雙重處理試樣的表面硬度則是隨載荷的增加而減小,而且,在同樣載荷下雙重處理試樣的硬度要比單一處理的高。同時從不同載荷下兩種處理試樣顯微壓痕形貌觀測(見表1)結果發現,在較低載荷下(10g~300g),兩類試樣壓痕周圍和內部都無明顯的裂紋出現,而當載荷較高(500g、1000g)時,單一處理試樣壓痕內部出現較多巢狀裂紋(圖2),而雙重處理試樣則較少。

顯然,在Cr12MoV鋼上沉積Ti/TiN涂層提高了材料的表面承載能力,特別是雙重處理。這是因為在較小載荷(如10g)作用下,涂層-基體體系是以涂層的塑性變形為主的,承載能力主要來自于硬、韌的Ti/TiN涂層,所以單一處理和雙重處理試樣顯示出高的顯微硬度值,壓痕周圍無明顯的裂紋出現。隨著載荷的增大,基體對測試硬度的影響逐漸增大,雙重處理試樣因有基體離子氮化產生的強化層對涂層的有力支撐作用,因而顯示出比單一處理試樣更好的承載能力,而且,離子氮化減少了涂層-基體界面大的應力梯度,因此在高載荷如1000g下,壓痕周圍顯示比單一處理試樣少的巢狀裂紋。

3.2 劃痕試驗
圖3是單一處理和雙重處理試樣的劃痕試驗結果(摩擦力-載荷曲線)。可以看出隨著載荷的增加,兩類試樣切向摩擦力基本都呈線形增加,單一處理的摩擦力更大一些,而且兩者都沒有出現摩擦力突然增大的峰值。單一處理試樣摩擦系數大約保持在0.2左右(摩擦力-載荷曲線的斜率μ=F/N),而雙重處理試樣約為0.15。
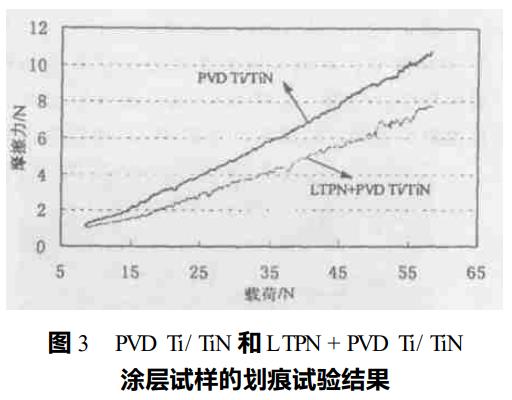
因摩擦力-載荷曲線沒有顯示出突然增大的摩擦力峰,顯然,涂層還沒有發生完全破壞,所以在Cr12MoV基體上沉積TiN涂層具有高的臨界載荷(Lc),即Lc大于60N,而且可以預測雙重處理有更高的臨界載荷,因為離子氮化過程產生的離子濺射效應,會使基體表面產生微觀的凹凸不平,因此增加了TiN涂層與基體的機械鉗合作用;其次Fe、N、Cr、Ti內擴散層的形成和對界面應力梯度的降低,也對結合力提高起到影響;而且由于中間硬化層的效應,TiN裂紋的擴展只有在基材界面上才能進行,延長了裂紋移動路徑,因此大大增加了TiN結合力。
3.3 磨損試驗
為了更好地評價在Cr12MoV鋼基體上單一處理和雙重處理涂層的耐磨性,本實驗采用高淬高回(未表面處理)Cr12MoV鋼作為對比材料。表2是三種試樣不同磨損時間下的磨損體積。從表2中可以清楚地看到,單一處理和雙重處理后試樣的磨損量明顯低于未表面處理試樣。當磨損9h時,未表面處理試樣的磨損量是單一處理試樣的14倍左右,是雙重處理試樣的23倍左右。很明顯,經表面處理后試樣耐磨性都得到了提高,特別是經過雙重處理的耐磨性更好。

圖4、5、6是三種試樣磨損形貌的低倍照片及SEM細節,可以看出未表面處理試樣磨損形貌為典型的犁溝(見圖4a),而且高倍的SEM照片也顯示了嚴重的犁溝(見圖4b),而經表面處理的試樣磨損形貌都為非常光滑的表面,即無明顯的塑性流動、微裂紋和脆性的跡象(見圖5和圖6)。

通常,材料的硬度越高,耐磨粒磨損性能越好。在滑動磨損試驗過程中,未表面處理試樣的Ha/Hm值(這里Ha指對磨試樣表面硬度,Hm指上試樣表面硬度)約為1.5左右,因此按M.M赫魯曉夫的結論,試樣會產生嚴重的平行于滑動方向的犁溝,同樣,對于表面處理過的試樣,Ha/Hm約為0.4,對磨試樣硬的粗糙峰對上試樣只是起到拋光作用,所以,試樣顯示出比較光滑的磨痕。而且從磨損形貌看(圖5b和圖6b),雙重處理顯示比單一處理更光滑的磨損表面,這主要歸因于離子氮化提高了材料的表面承載能力和涂層與基體的結合強度,降低了磨損過程中表面和次表面的剪切變形,使涂層在一定外加載荷沖擊作用下不易剝落而造成三體磨粒磨損。
3.4 應用試驗
對經PVD Ti/TiN單一處理的模具進行了實際應用試驗,該冷沖模具實際使用壽命由原來的約2500次增加到6650次,即模具實際使用壽命提高了2倍多,而且從模具磨損后的失效形貌發現磨損部位為光滑的表面,屬于逐漸磨損,沒有出現涂層剝落的痕跡,這與試樣的磨損試驗結果相一致。
4、結論
(1)在Cr12MoV鋼上沉積Ti/TiN涂層能顯著地提高Cr12MoV鋼的表面硬度及承載能力。而且,先進行低溫等離子氮化處理的雙重處理更能改善涂層-基體結合條件,顯著提高涂層與基體的結合強度,這歸因于Ti/TiN涂層強化和韌化的作用以及中間氮化層的強化作用。
(2)硬、韌和低摩擦系數的Ti/TiN涂層大大地提高了Cr12MoV鋼的耐磨性,與未經表面處理試樣比較,單一處理和雙重處理試樣磨損形貌都為比較光滑的表面,而且在磨損時間相同的條件下,雙重處理比單一處理有更少的磨損量。
聲明:本站部分圖片、文章來源于網絡,版權歸原作者所有,如有侵權,請點擊這里聯系本站刪除。
返回列表 | 分享給朋友: |